How many of you can identify
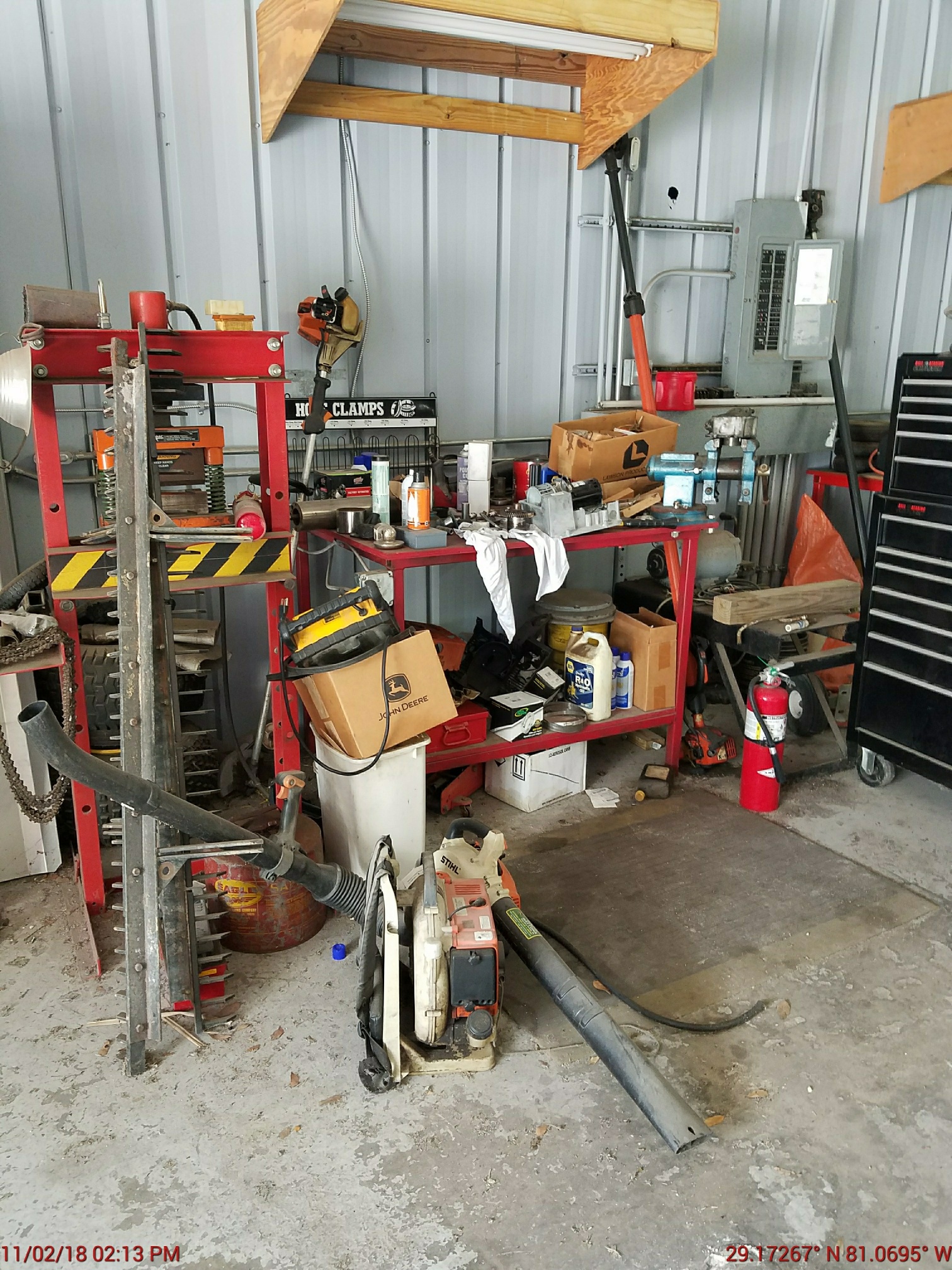
with this scenario?
You have staff scheduled to drag your ball field for an important softball tournament and the infield machine won’t start. They determine it is a safety switch that needs adjusted. They go to your trusty shop toolbox and look for the 9/16ths socket w/ 1/2” drive with the extension and the universal to reach the adjustment to make the adjustment. But when they look for it, they can only find a 9/16th socket in the 3/4” drive. Ok, so they have to use a tool bigger than they need, no big deal right? Only to realize they don’t have a universal attachment for a 3/4” drive to help reach the bolt to adjust the safety switch to get the infield drag operational!
The universal joint was used yesterday to help make a repair to the lift station and was dropped down into the vault. So they decide with the tools they have to remove the seat, seat frame, and two other hose clamps to be able to access the bolt that is now becoming the needle in the proverbial haystack. As the supervisor, you realize the field still hasn’t been dragged and find maintenance staff fully involved in a mechanical operation that has taken on a life of its own. Sometimes the smallest things can trip up your operations and give you pause. Getting to the root of the problem may be right under your nose, or feet as it were. Not only may your toolbox not have all the correct tools you need but they may be so scattered it takes way too much time to find them or account for them.
Back away from the toolbox and look at your maintenance facility. If you have tools on the floor, power tools laying on your workbench, rakes, and shovels leaning in the corner waiting for someone to step on them and re-create a three stooges short, you may have found the problem. Organizing you maintenance facility can take many hours and some creative thinking of how to store and track your tools & equipment.
However, the time invested in creating a well-organized and maintained maintenance facility over the long run can make your crews more productive and efficient than even they thought possible. Space seems to often be an obstacle. You may have opportunities to use the walls to hang equipment to free up floor space. Rafters are also an opportunity for storage. If you simply do not have any more space, it may be worth looking at how the space is being utilized. A re-organization can also produce better results. Heated vs cold storage should also be considered. An outdoor roof or simple lean-to may be just the ticket for those items that can safely be stored outside.
One of my favorite things to do is visit other facilities and not just park facilities to see how others organize their maintenance facilities. Schools, Ballparks, Commercial Landscapers, Cities, Counties, State Facilities, Commercial Facilities. Chances are you know many of these folks and many would be willing to have you visit. Take pictures and ask questions, there’s a good chance some of the best ideas they have were either from their own staff or from other facility operators. And don’t forget to put that 9/16ths socket back where you found it!
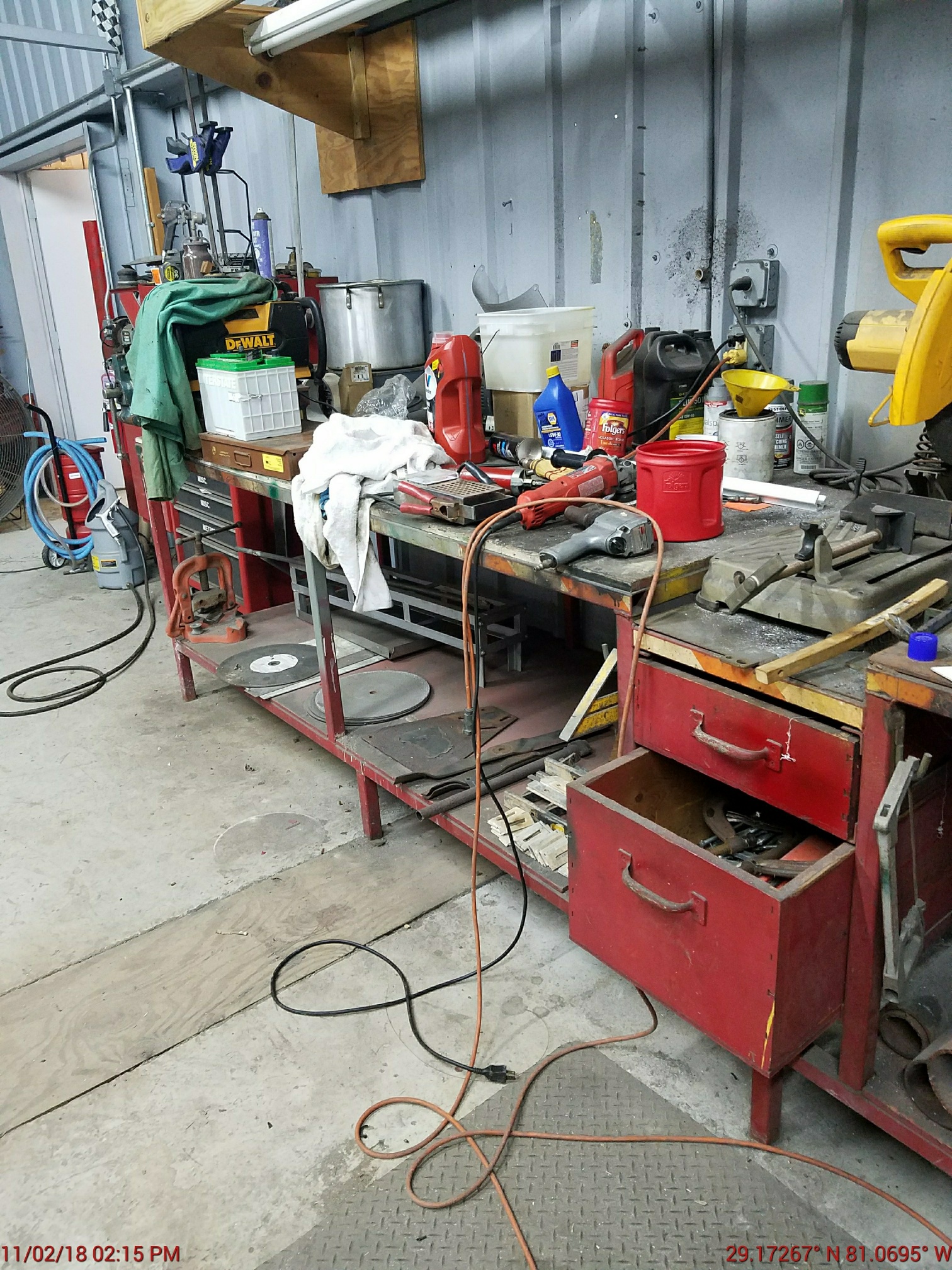